Understanding Injection Molding Tools for Metal Fabrication
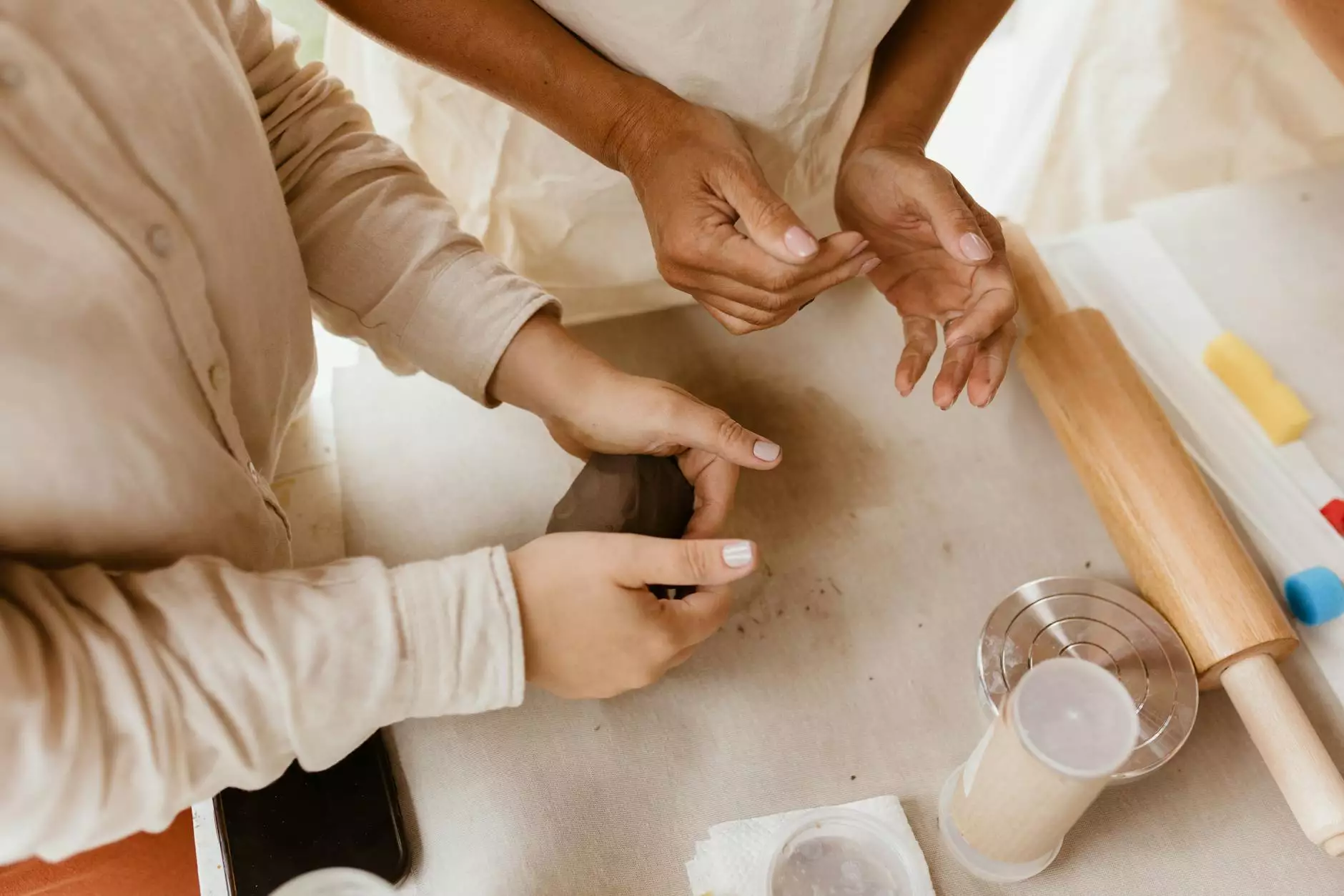
In the ever-evolving landscape of manufacturing, injection molding tools stand out as a pivotal technology, especially when it comes to metal fabrication. Understanding these tools can unlock new opportunities and efficiencies for businesses looking to innovate and enhance their production capabilities.
What are Injection Molding Tools?
Injection molding tools are specialized equipment designed to create objects by injecting molten material into a mold. This process can apply to various materials, including metals, plastics, and composites. In the context of metal fabrication, injection molding has gained traction due to its ability to produce complex and precise components with minimal waste.
History of Injection Molding
The concept of injection molding originated in the early 19th century, but it was not until the mid-20th century that it became widely adopted in the manufacturing sector. Over the decades, injection molding has evolved significantly, incorporating advancements in materials and technology that allow for greater precision and efficiency.
The Role of Injection Molding in Metal Fabrication
Within the realm of metal fabrication, injection molding tools serve several critical roles:
- Cost-Effectiveness: Reduces production costs by minimizing material waste.
- Precision Engineering: Ensures high accuracy in complex designs.
- Scalability: Facilitates high-volume production without sacrificing quality.
- Material Versatility: Supports a variety of metals and alloys, catering to specific project requirements.
Advantages of Using Injection Molding Tools
The advantages of employing injection molding tools in the metal fabrication industry are numerous. Here are some of the most notable benefits:
1. Enhanced Production Speed
The injection molding process is known for its speed. By using well-designed molds, manufacturers can produce thousands of parts with minimal cycle time. This increased production rate can significantly enhance overall productivity.
2. Superior Surface Finish
Parts produced through injection molding often exhibit a superior surface finish compared to those made using traditional machining techniques. This is essential for components that require a high aesthetic value or functionality.
3. Reduction of Labor Costs
Automating the injection molding process means that fewer labor resources are needed. This reduction in labor not only cuts costs but also minimizes human error, leading to improved consistency in production quality.
Key Components of Injection Molding Tools
To fully understand how injection molding tools function, it's important to familiarize yourself with their key components:
- Mold: The core of the injection molding process, where the material is shaped.
- Injection Unit: Responsible for melting the material and injecting it into the mold.
- Clamping Unit: Holds the mold in place during the injection process to withstand the pressure of the injected material.
- Cooling System: Allows the molded part to solidify by controlling the temperature within the mold.
- Control System: Manages the operational parameters of the molding machine for optimal performance.
Innovations in Injection Molding Technology
As the manufacturing sector continues to advance, so too does the technology behind injection molding tools. Recent innovations include:
1. Advanced Materials
The development of new materials, such as metal-polymer composites, has expanded the range of applications for injection molding. This advancement allows manufacturers to produce parts that are stronger yet lighter than traditional materials.
2. 3D Printing Integration
3D printing technologies are being integrated with injection molding processes to create complex molds more quickly and efficiently. This hybrid method reduces lead times and enhances design flexibility.
3. Smart Injection Molding
Smart technology and the Internet of Things (IoT) are starting to play a role in injection molding, allowing for greater monitoring and control over the process. This can lead to predictive maintenance and improved production accuracy.
Applications of Injection Molding in Metal Fabrication
The applications of injection molding tools in metal fabrication are vast and varied. Here are some notable examples:
- Automotive Industry: Parts such as brackets, clips, and housings.
- Aerospace Sector: Components that require high strength-to-weight ratios.
- Consumer Electronics: Precision parts for devices such as smartphones and laptops.
- Medical Devices: Intricate components used in life-saving equipment.
Challenges in Injection Molding
While injection molding tools offer numerous advantages, there are also challenges that manufacturers must navigate:
1. Initial Costs
The upfront costs for designing and manufacturing molds can be significant. However, these costs are often offset by the long-term savings in production.
2. Maintenance of Molds
Molds require regular maintenance to ensure they continue to function correctly over time. Neglecting this aspect can lead to defects in the molded parts.
3. Material Limitations
Not all materials are suitable for injection molding, and selecting the wrong material can lead to failures during the production process.
How to Choose the Right Injection Molding Tool
Choosing the correct injection molding tool for your business requires careful consideration of several factors:
- Project Specifications: Understand the specific requirements of your project, including dimensions and tolerances.
- Material Selection: Research which materials are best suited for your needs.
- Production Volume: Determine the expected production volumes to choose the right type of molding system.
- Supplier Expertise: Select suppliers with a proven track record and expertise in the specific area of injection molding.
Conclusion
In conclusion, injection molding tools represent a cornerstone of modern metal fabrication. They provide immense benefits in terms of cost-efficiency, speed, accuracy, and adaptability. As technological innovations continue to emerge, the potential applications of these tools will only broaden, allowing businesses like Deep Mould to thrive in a competitive market.
By leveraging the advantages of injection molding and staying abreast of industry advancements, forward-thinking companies can position themselves not only for success in the present but also for sustainable growth in the future.