Revolutionizing Metal Fabrication with **Prototype Moulds**
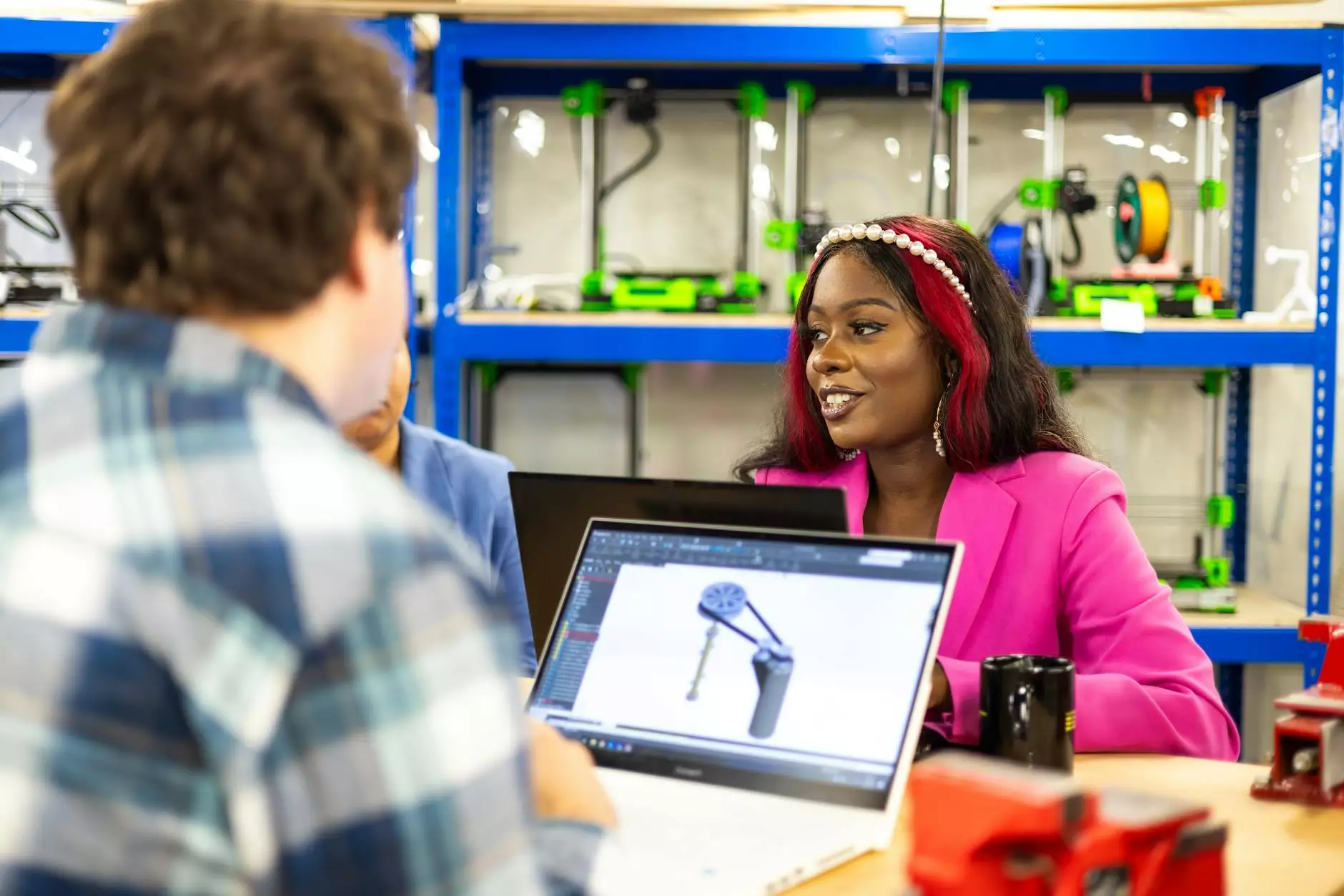
In today's fast-paced manufacturing landscape, the demand for innovation and efficiency is at an all-time high. The advent of prototype moulds has changed the game for many businesses, particularly in the sector of metal fabrication. As companies seek to streamline processes, improve product quality, and reduce time-to-market, understanding the critical role of mould prototyping is essential. At Deep Mould, we embrace this technology to drive transformation and excellence in our services.
The Importance of Prototype Moulds in Metal Fabrication
Prototype moulds serve as a cornerstone in the metal fabrication industry. These are specialized tools designed to create prototypes of products, allowing businesses to test designs before full-scale production begins. This process not only mitigates risks but also fosters innovation. Here’s why prototype moulds are integral:
- Cost Efficiency: By identifying design flaws early, companies can avoid costly modifications during mass production.
- Faster Time-to-Market: Prototyping allows for rapid iterations of designs, greatly reducing the overall time needed to launch new products.
- Enhanced Product Quality: Testing prototypes under real-world conditions helps refine product quality before it reaches consumers.
- Risk Mitigation: Using prototypes to experiment with designs decreases the likelihood of production errors and subsequent financial losses.
Understanding the Process of Creating Prototype Moulds
The journey of a prototype mould begins with a robust design phase. It is critical to conceptualize a design that not only aligns with the product’s functionality but is also feasible for manufacturing. Here’s an overview of the typical process:
1. Concept Development
Every successful prototype begins with an idea. Designers brainstorm and sketch initial concepts, focusing on how the product will function and look.
2. Digital Modeling
Once a concept is settled, CAD (Computer-Aided Design) software is used to create detailed 3D models. This stage allows for the visualization of the prototype before it is produced.
3. Prototype Fabrication
The next step involves the actual creation of the prototype mould. Techniques like 3D printing or CNC machining are commonly employed to produce an accurate model that can withstand testing.
4. Testing and Evaluation
Once fabricated, the prototype undergoes rigorous testing to evaluate its performance. Feedback during this phase is crucial for identifying areas for improvement.
5. Final Adjustments
After testing, adjustments are made to optimize the design. This iterative process may repeat several times until the prototype meets the desired specifications.
Applications of Prototype Moulds in Various Industries
The versatility of prototype moulds means that they find applications across multiple industries. At Deep Mould, we cater to various sectors including:
- Aerospace: Developing complex components that meet stringent safety standards.
- Automotive: Creating parts that improve vehicle performance and efficiency.
- Consumer Electronics: Designing enclosures and internal components that enhance user experience.
- Medical Devices: Crafting precision instruments that must comply with regulatory requirements.
Case Study: Innovation in Automotive Prototyping
One significant case where prototype moulds made a marked difference was in the automotive industry. A leading car manufacturer partnered with Deep Mould to develop a new line of fuel-efficient vehicles. By investing in prototype mould technology, the company successfully:
- Reduced the weight of their vehicles while maintaining structural integrity.
- Improved fuel efficiency through aerodynamically optimized parts.
- Decreased production costs by streamlining the design process.
Benefits of Partnering with Deep Mould for Prototype Moulds
Choosing the right partner for your prototyping needs is essential. Here’s why Deep Mould stands out in the metal fabrication landscape:
1. Expertise and Experience
With years of experience in manufacturing and prototyping, our expert team is equipped to handle projects of any scale. We possess a deep understanding of various industries, ensuring that we deliver solutions tailored to your specific requirements.
2. State-of-the-Art Technology
At Deep Mould, we leverage the latest technology in CNC machining, 3D printing, and other advanced fabrication techniques. This commitment to technology ensures that your prototypes are not only accurate but also innovative.
3. Commitment to Quality
Quality is our top priority. Every prototype mould produced by Deep Mould undergoes strict quality control measures to ensure compliance with international standards.
4. Collaboration and Support
From the initial consultation through to project delivery, we work closely with our clients, providing support and guidance at every stage. Our collaborative approach fosters strong partnerships and results in successful outcomes.
Future Trends in Prototype Mould Technology
As we look towards the future, several trends are shaping the evolution of prototype moulds and the broader metal fabrication industry:
- Increased Automation: The rise of automation in manufacturing processes will enhance efficiency and reduce human error.
- Sustainability Practices: More companies are focusing on sustainable materials and processes to minimize environmental impact.
- Integration of AI: Artificial intelligence is increasingly being integrated into design and manufacturing processes, allowing for smarter decision-making based on data analytics.
- Advanced Materials: Innovations in materials science are leading to the development of lighter, stronger, and more durable materials for use in prototype moulds.
Conclusion: Embrace the Future with Prototype Moulds
In conclusion, prototype moulds play a vital role in today’s manufacturing environment, especially within the realm of metal fabrication. By embracing this technology, businesses can achieve greater efficiency, reduce costs, and foster innovation. As a leader in the metal fabricators category, Deep Mould is committed to providing state-of-the-art solutions and exceptional service to propel your business forward.
We invite you to explore how our prototype moulds can transform your projects and ensure that you stay ahead of the competition. Contact us today to learn more about our services and discover the Deep Mould advantage.